The universal double-girder bridge crane is a crane that runs on a track across the factory building. Bridge hook (lifting hook) cranes use hooks as retrieval devices. They are suitable for loading, unloading and lifting work within the fixed spans of workshops and warehouses of general industrial and mining enterprises. Various types of general double-girder bridge cranes may occur during use. Such a fault, so how do we solve it?
The brake cannot hold the brake wheel
Cause of failure: 1. The hinge of the lever is stuck. 2. There is oil on the brake wheel and friction plate. 3. The electromagnet core has no stroke. 4. The brake wheel or friction plate is severely worn (a basic type of component failure). 5. The main spring (Spring) is loose and damaged. 6. The locking nut is loose and the tie rod is loose.
Troubleshooting methods: 1. Lubricate and eliminate stuck faults. 2. Clean oil stains. 3. Adjust the brake 4. Replace the friction plate. 5. Replace the main basket and locking nut. 6. Tighten the locking nut. 7. Inspect the impeller (referring to the disc equipped with moving blades) driving mechanism.
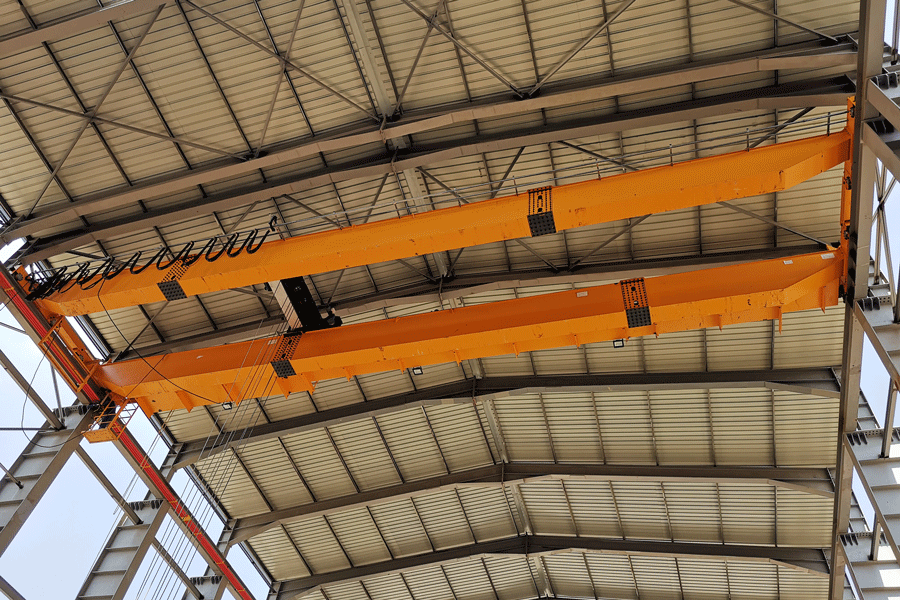
The brakes heat up, and the friction plates smell burnt and wear out quickly (a basic type of component failure).
Reasons for the failure: 1. After the brake is released, the brake shoe does not fully detach from the brake wheel evenly, thus causing friction. Single girder crane has two operation modes: ground and aerial. There are two types of ground operations: wired handle operation and remote control handle operation; aerial operation refers to driver’s cab operation. The driver’s cab has two types: open type and closed type. It can be divided into two types: left or right installation according to the actual situation. There are two entrance directions: side and end, to meet the user’s choice under various needs. 2. The gap between the two brake shoes and the brake wheel is uneven, or the gap is too small. 3. The short-stroke brake auxiliary spring (Spring) is damaged or bent (Bend). 4. The working surface of the brake wheel is rough.
Remove method: 1. Adjust the gap. 2. Adjust the gap. 3. Replace or repair the auxiliary spring (Spring). 4. Process the brake wheel surface as required.
The reducer (divided into gear reducer, worm reducer, etc.) has uneven knocking sound when the gear meshes, and the casing vibrates.
Cause of failure: The tooth surface is defective, and the gear teeth are not in contact along the entire tooth surface but in one corner. Single girder crane has two operation modes: ground and aerial. There are two types of ground operations: wired handle operation and remote control handle operation; aerial operation refers to driver’s cab operation. The driver’s cab has two types: open type and closed type. It can be divided into two types: left or right installation according to the actual situation. There are two entrance directions: side and end, to meet the user’s choice under various needs. Single girder crane usually refers to single girder overhead crane. The main beam of single-girder crane bridge mostly adopts I-shaped steel or a combined section of steel profile and steel plate. Lifting trolleys are often assembled with hand chain hoists, electric hoists or hoists as lifting mechanism components.
Troubleshooting: Replace the gear.
The reducer housing, especially where the bearings are installed, generates heat.
Cause of failure 1. The bearing is broken. 2. The journal is stuck. 3. Gear teeth are worn. 4. Lack of lubricating oil.
Remove method: 1. Replace the bearing. 2. Replace the bearings. 3. Trim the gears. 4. Change lubricating oil
The wire ropes of universal double-girder overhead cranes wear out quickly or are often damaged.
Cause of failure 1. The diameter of the pulley and drum is too small. 2. The size of the rope groove on the drum does not match the rope diameter and is too small. 3. There is dirt and lack of lubrication. 4. The lifting limit baffle is not installed correctly and the rope is often worn. 5. The bottom of the pulley groove or the rim is not smooth and defective.
Removal method: 1. Replace the flexible wire rope (composed of steel wire, rope core and grease) or increase the diameter of the pulley or drum. 2. Replace the wire rope with the same lifting capacity but smaller diameter, or replace the pulley and drum. 3. Clean and lubricate. 4. Reinstall. 5. Eliminate defects.
The crane bridge is running skewed
Cause of failure: 1. The diameter error of the two driving wheels is too large. 2. The driving wheels are not in direct contact with the track. 3. The axis of the driving wheel is incorrect. 4. Deformation of metal structure. 5. The track installation quality is poor. 6. There is oil stain on the rail top
Removal method: 1. Measure and replace the wheel. 2. Drive the fully loaded trolley to the end behind the trolley. If the trolley goes straight, it means that the driving wheel at this end is not in contact with the track and the wheel pressure is small. The diameter of the driving wheel at this end can be increased. 3. Check and eliminate axis deflection and correct it. 5. Adjust the shaft track to make the track meet the standards. 6. Eliminate oil stains.
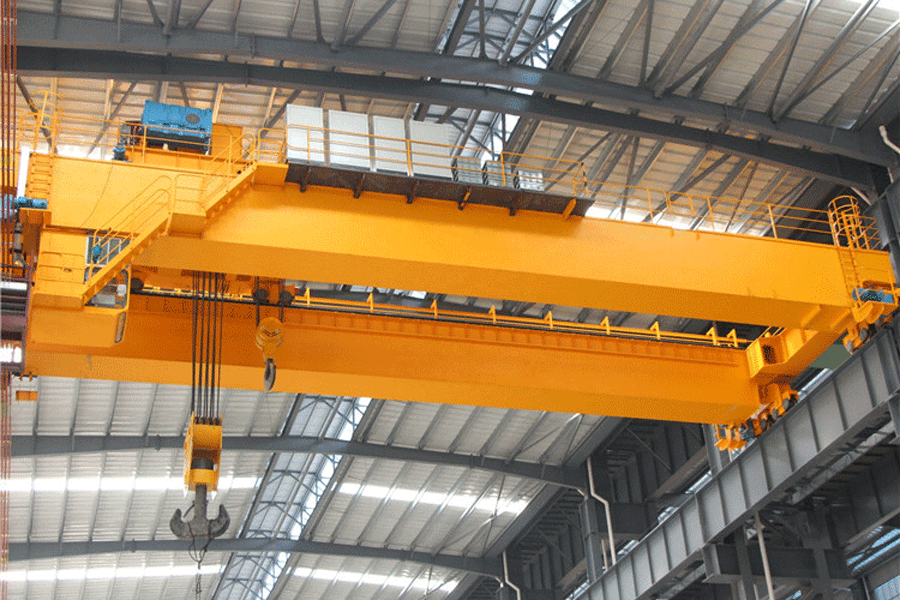
General double-girder bridge crane trolley slips while traveling
Causes of failure: 1. Oil stains on the track, etc. 2. Different wheel pressures. 3. The elevation difference between the two tracks in the same section is too large
Elimination methods: 1. Eliminate. 2. Adjust wheel pressure. 3. Adjust the track.
Universal double-girder bridge crane operates on three legs
Reasons for the failure: 1. The wheel diameter deviation is too large 2. The installation is unreasonable. 3. The small frame is deformed.
Troubleshooting methods: 1. Process the wheels as required. 2. Readjust the installation according to technical conditions. 3. Frame correction.