Compared with general cranes, intelligent overhead cranes have artificial intelligence, which replaces or assists human mental labor on the basis of replacing human physical labor. By integrating sensors with intelligent decision-making software and cranes, perception, analysis, reasoning, decision-making, and control are achieved
Function, achieving interaction and integration between humans and objects, replacing manual perception, decision-making, and execution, enabling the crane to adapt to changes in the working environment. Its workflow is the same as that of a general crane, but the added intelligent control can replace human vision, hearing, and smell
sensory organs such as the senses and limbs replace the operator’s judgment to make corresponding actions, completing recognition, perception, operation, and management during the operation of the crane.
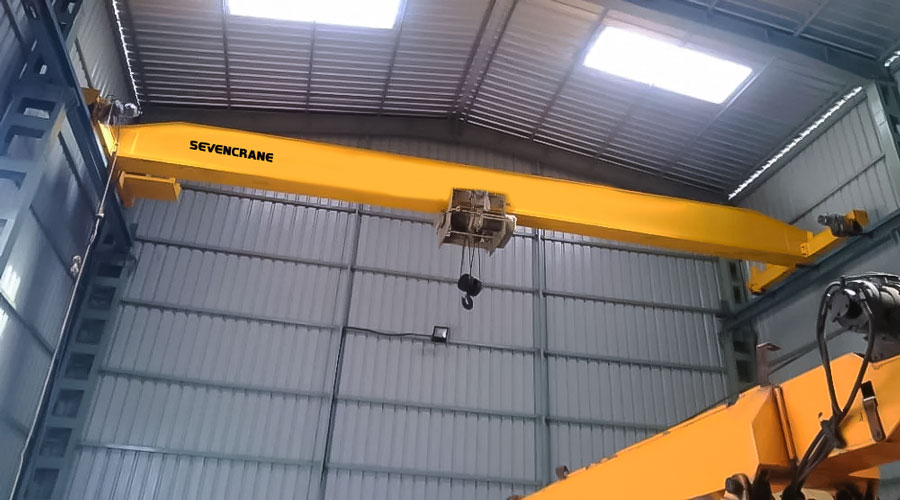
Key Technologies of Intelligent Cranes
In the process of perception, decision-making and execution on behalf of the operator, the crane needs to automatically sense the location of the lifted items, automatically identify and verify the lifted items, automatically pick up and place the lifted items, automatically select the operating route, automatically optimize the operating route and overcome The swing of the flexible lifting system can accurately start and stop the items stored in the corresponding positions, and record and monitor the working status of its own equipment during automatic operation, automatically diagnose faults and alarm. Therefore, the artificial intelligence of cranes needs to break through several key technologies.
Item identification, verification, feedback and information storage technology
According to the shape, packaging method, storage and transportation method of the items to be lifted, common items to be lifted include: rolls (steel coils, paper rolls, film rolls, etc.), boxes (containers, material boxes, transfer boxes, etc.), blocks (steel plates, Steel blanks, shield members, etc.), bundles (steel pipes, rebars, rails, shaped steel, etc.), discs (cables, wire rods, etc.), pieces (buckets, bags, etc.), roots (rails, I-beams, H-shaped steels, etc.), etc.).
The automatic identification, inspection and feedback of items in various states are standardized means of data encoding, collection and identification management, and transmission, and are the basis for intelligent crane work. This technology involves the encoding, collection, identification, management, and transmission of item information data. Including barcode recognition, RFID radio frequency recognition, speech recognition, optical character recognition, magnetic recognition and other specific format information recognition technologies and image, graphic recognition, biometric recognition and other image and graphic format information recognition technologies. The item information stored after identification and inspection must be universal, unique, stable and non-replicable.
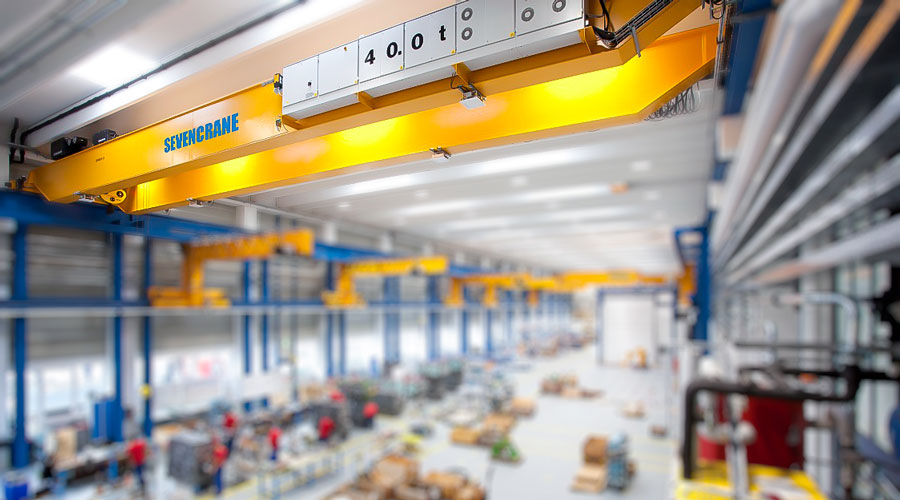
Spatial positioning technology
Although some high-end domestic products apply three-dimensional positioning technology, the positioning level is limited by the cumulative error of the entire machine system and cannot achieve high-precision positioning. At present, there are two types of commonly used positioning methods: one is relative addressing, which is generally implemented by rotary encoders, laser or radar ranging, visual recognition, etc.; the other is absolute addressing, which is generally implemented using position limits. Switches, coding cables (Gray bus), linear encoders, BPS barcodes, sprocket chains, and real-time absolute addressing radio, infrared, wireless radio frequency, GPS, etc. are implemented. With the advancement of wireless communication technology, the positioning accuracy of cellular positioning of communication networks and indoor wireless positioning technologies such as Wi-Fi, Bluetooth infrared, ultra-wideband, RFID and ultrasound has become increasingly higher, and has been gradually promoted and applied in the positioning of mechanical equipment.
Crane positioning technology not only involves appearance monitoring, vacancy detection, and one-dimensional, two-dimensional, and three-dimensional identification and positioning methods of the actual storage location of the lifted items, but also involves overhead crane retrieval devices (hooks, cargo racks, suction cups, grabbers, etc.) Grab bucket, etc.) one-dimensional, two-dimensional, and three-dimensional address recognition and positioning methods.
Due to the large operating range of the crane, it is difficult to achieve the required positioning accuracy with a single positioning method. Therefore, the comprehensive positioning technology of “relative approach addressing + absolute positioning” is often used for precise positioning in large areas and complex environments. Compared with the simple absolute address recognition or relative address recognition and positioning methods, it is more accurate, more stable, more economical, has lower requirements on the quality of civil engineering projects, and is more suitable for harsh environments with lifting equipment.
Intelligent object retrieval device
More than 95% of crane retrieval devices use hooks, which can only be lifted manually to lift a specific type of items. The versatility is poor, which restricts the improvement of automation of lifting and handling equipment. In the process of lifting and carrying different items such as bulk materials, boxes, bundles, rolls, etc., smart cranes need to be equipped with automatic picking devices or smart spreaders, including automatic lifting hooks, C-shaped hooks, electromagnetic suction cups, vacuum suction cups, and Clamps, hanging beams, box spreader tanks, grab buckets, grabbers, etc. According to the status of various hoisted objects, developing automatic retrieval devices or intelligent spreaders suitable for crane applications to achieve automatic access to the crane is the most critical link for the crane to become intelligent.
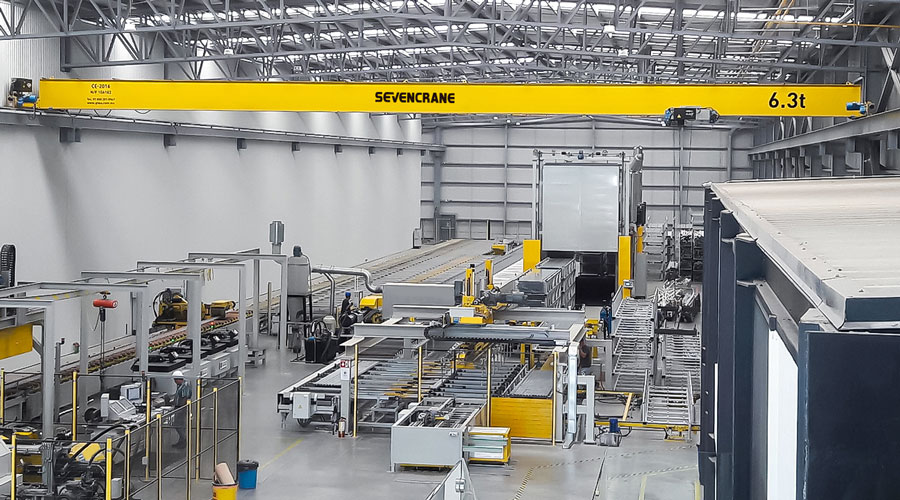
Electronic anti-sway technology for path planning and flexible lifting systems
Operation path planning and anti-sway positioning control of the flexible lifting system are necessary conditions for crane operation. During the operation of the crane, the acceleration and deceleration of large and small trucks and the lifting of the load will cause the load to swing back and forth, which will not only affect the operating efficiency of the crane, but also cause accidents. Currently, open-loop and closed-loop control technologies are commonly used to implement crane path planning and anti-sway control. The open-loop control method mainly includes positioning anti-sway control based on input shaping and positioning anti-sway control based on trajectory planning. There are many closed-loop control methods to achieve path planning and anti-sway, such as feedback linearization, gain scheduling control, sliding mode control, predictive control, fuzzy control, neural network control, passive control and other control methods.
For hoisting and handling environments where obstacles are fixed, static path planning can meet the requirements. However, when obstacles in the environment cannot be determined in advance or when multiple cranes are operating in a mixed manner, a dynamic path planning method needs to be used to obtain a safe path online in real time. Hoisting path planning. In recent years, scholars have proposed some effective planning algorithms for crane path planning, such as artificial potential field method, probabilistic landmark algorithm, fast random spanning tree algorithm, genetic algorithm, ant colony algorithm, etc.
With the development of wireless mobile communication technology, sensors (gyros, acceleration sensors, orientation sensors, etc.) are installed on hoists or fetching devices to realize three-dimensional positioning, path planning and anti-sway control based on the hoisted objects. Be widely used.
Status detection and automatic fault diagnosis technology
Condition monitoring refers to understanding and mastering the operating status of equipment through certain channels; fault diagnosis is based on the information obtained from condition monitoring, combined with the working principle, structural characteristics, operating parameters, and historical conditions of the equipment, to analyze possible faults. , Forecasting, analyzing and judging faults that have occurred or are occurring to determine the nature, category, extent, location and trend of the fault. The significance of condition monitoring and fault diagnosis is that it effectively curbs fault losses and equipment maintenance costs.
Common monitoring parameters that need to be monitored during the hoisting machinery monitoring process include lifting weight, gravity moment: lifting height/descent depth; operating stroke, amplitude, truck operating deflection; levelness; wind speed; rotation angle; same or different 1. Safety distance of the track running mechanism; verticality of the outriggers; working time, accumulated working time, each working cycle, etc. Commonly used monitoring status includes motor status; brake status; frequency converter status; wind resistance and anti-skid status; interlock protection door limit and operating interlocking between mechanisms; working condition setting status; power supply cable reel status; via hole status; To absorb the video system, bridge stiffness, strength real-time self-detection system, etc.
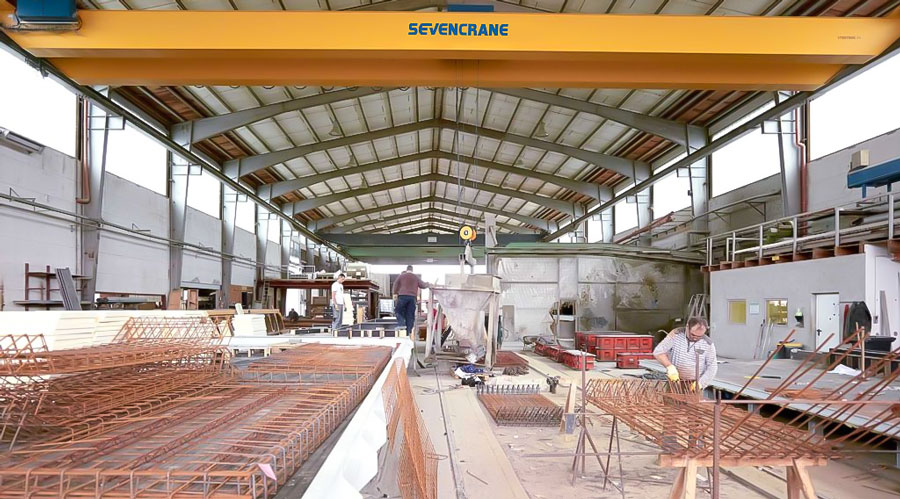
Real-time online monitoring and remote diagnosis technology
The system includes sensor monitoring, real-time wireless transmission, data management, information query, fault root cause analysis, trend analysis, expert diagnosis, status prediction and prediction, Internet of Things remote monitoring and other technologies. By installing monitoring gateways on existing equipment, data is transmitted through Wi-Fi or 3G networks to collect operating status and fault conditions to achieve remote monitoring and visual management; integrate the remote management system that comes with new equipment to establish a unified equipment management platform; and Asset maintenance management system integration improves maintenance efficiency and equipment performance. Provide a networked emergency maintenance coordination and cooperation mechanism, obtain the real-time status of equipment through wireless meter reading, automatically generate maintenance and inspection plans, and gradually implement status-based predictive maintenance based on data analysis.
Predictive maintenance realized through computer network is based on condition monitoring and fault diagnosis technology, based on the actual condition of the equipment, and a maintenance system that develops predictive maintenance plans according to production needs. The goal is to achieve real-time parking, corresponding parts replacement, and maintenance of confirmed projects. From the current fault maintenance and regular planned maintenance, we can realize future predictive maintenance, identify the authenticity of the fault, determine the type, degree and specific location of the fault, and predict the development trend of the fault. Detect early signs of failure in a timely manner so that appropriate measures can be taken to avoid, slow down, and reduce the occurrence of major accidents; – Once a failure occurs, complete information about the failure process can be automatically recorded for subsequent analysis of the cause of the failure to avoid similar occurrences again. Accidents; through the analysis of the abnormal operating status of equipment, reveal the cause, degree, location and trend of the failure, provide scientific basis for online conditioning and shutdown maintenance of equipment, extend the operating cycle, and effectively curb failure losses and equipment maintenance costs; according to the status The information obtained from monitoring is combined with the working principle, structural characteristics, operating parameters, and historical conditions of the equipment to analyze and predict possible failures, which can fully understand the equipment performance and provide strong evidence for improving design, manufacturing, and maintenance levels.
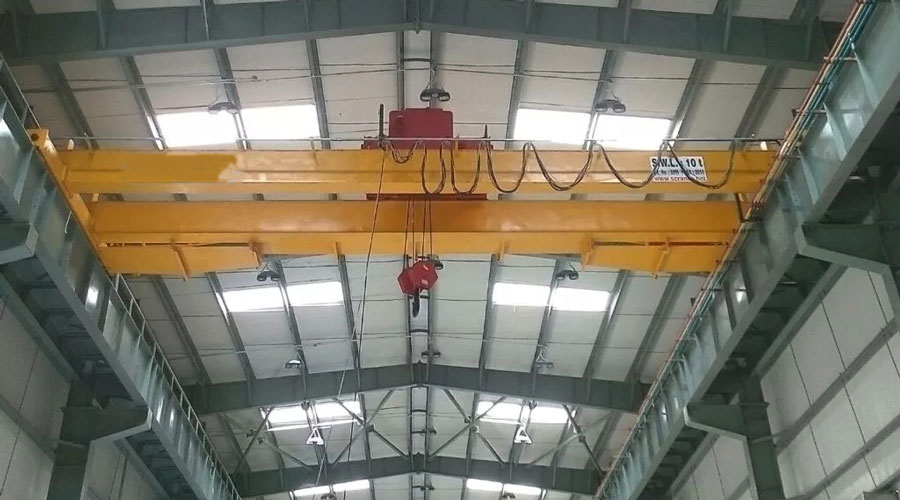
Based on the stacking forms and storage requirements of different items such as bulk materials, boxes, bundles, rolls, etc., a monitoring and management system MWS for intelligent cranes is developed based on the above key technologies such as identification, positioning, access, and monitoring, including interface subsystems and cargo space inventory. Management subsystem, item identification subsystem, dispatching and crane operation subsystem, spatial positioning subsystem, etc., realize the intelligent, efficient and safe operation of the crane.
In Conclusion
The demand for various intelligent cranes in intelligent manufacturing, intelligent logistics, intelligent maintenance and other fields is increasing day by day, and the application prospects are broad. The above key technologies will be integrated into intelligent crane application solutions in the form of software, new products, new technologies, etc. to form a complete set of equipment for engineering, which can be used for station transfer in metallurgy, papermaking, automobiles and other intelligent manufacturing fields, and in the logistics field. Warehousing and moving. The intelligent crane automatically completes the operation of the process flow and can monitor and record the operating status of the crane in real time, providing higher work efficiency and lower operating costs. The intelligent monitoring and operating system implements intelligent maintenance services for in-service hoisting machinery, that is, through remote online detection and big data statistical analysis, predictive maintenance and remaining life assessment are achieved. The accumulated big data can provide data basis for the design of the crane, improve the overall design level of the crane, and effectively and targetedly improve the intrinsic safety and performance of the crane.