The SEVENCRANE rubber tyre gantry crane is the main equipment of the container terminal bridge. Currently, industrial rubber tyre gantry crane trolleys generally use rimless wheels and are designed with a guide device (horizontal wheel) added to one side of the track. This structural form reduces the manufacturing deviation and the impact of track gauge changes on the trolley operation under trolley load conditions. Rolling friction replaces sliding friction between the horizontal wheel and the side of the track, and the frictional resistance endured by the operating mechanism is greatly reduced.
However, in the actual operation process, the phenomenon of the trolley deviating from the track often occurs. That is, when the trolley is running back and forth, the center of the wheel seriously deviates from the center of the track, causing the horizontal wheel to squeeze the side of the track, increasing the friction between the two. This causes abnormal wear of the horizontal wheels and tracks, especially when the trolley travels at a full speed of 70 m/min, posing a major safety hazard to the trolley’s operation.

Danger of heavy duty rubber tyre gantry crane trolley running off track
1) When the trolley deviates, under the action of a large horizontal lateral force (resultant force), the self-aligning bearing inside the horizontal wheel will be overloaded and damaged, and even the entire horizontal wheel will break and fall, causing serious consequences.
2) The deviation of the trolley will increase the running resistance of the trolley, increase the power consumption of the trolley motor and the load of the mechanical transmission mechanism. In severe cases, it will cause the motor to burn out and the reducer to break the shaft, which increases daily maintenance costs.
3) When the trolley deviates, abnormal extrusion occurs between the horizontal wheel and the track, and between the wheel and the track, which shortens the service life of the track, generates impact loads on both the girder and the trolley, and produces horizontal lateral thrust transmission. If it is passed to the main structure, it will shake, and the main structure will easily deform and the welds will crack.
Reasons why the trolley deviated
Since the heavy duty rubber tyre gantry crane is in contact with the ground through flexible tires, the reasons for its trolley deviation are more complicated than those of conventional gantry cranes. In addition to design reasons, there are also reasons for manufacturing and use.
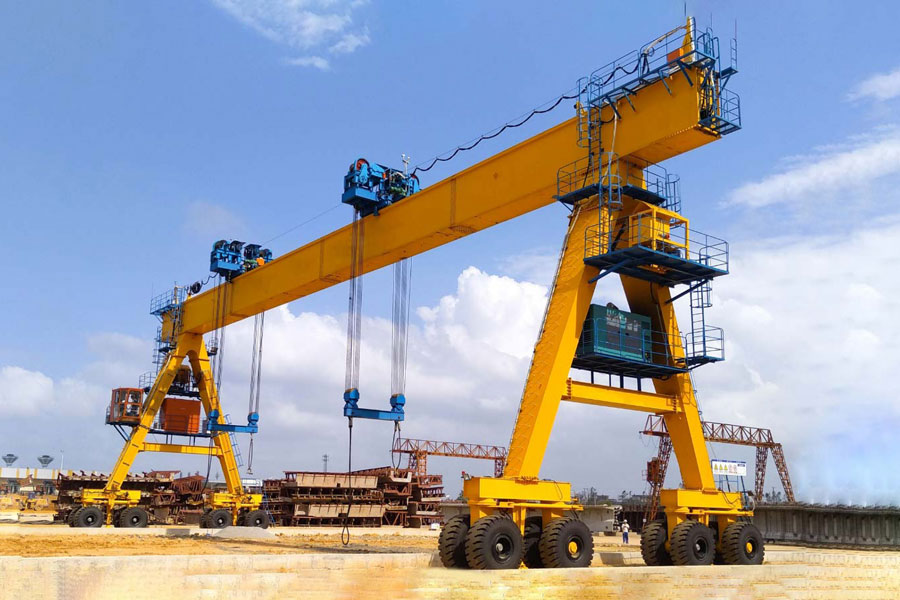
2.1 Reasons for manufacturing
1) If the track tread inclination exceeds the tolerance, it will cause the running wheels to shift sideways, causing the trolley to deviate. Longitudinal: 0.3%, transverse: 0.3%
2) If the diagonal deviation of the door frame is too large when assembling the door frame, it will cause the trolley to wander. The welding stress generated during the production of the steel structure will not be released until the RTG is used for a period of time, and certain deformation will also occur during the stress release process.
3) The height deviation ΔH of the trolley track in the plane perpendicular to the direction of movement of the trolley should not be greater than 0.15% of the track gauge K, and the maximum should not exceed 10mm. If the height deviation on both sides of the track is too large, the trolley will move laterally during operation, resulting in deviation.
4) The projection of the four wheel positions in the horizontal plane is not a rectangle, but a parallelogram or trapezoid. The co-location difference of the wheels on the same side of the track is greater than 2mm. In addition, the welding stress generated during the manufacturing process of the steel structure of the trolley will also produce a certain degree of deformation during the release process, causing the trolley to deviate.
5) When the trolley frame is in a horizontal position, the tread heights of the four wheels of the trolley should be on the same plane, and the height difference t of the wheels should not be greater than one thousandth of the track gauge K.
6) Installation deviation of the trolley wheels: horizontal deflection p ≤ (0.4/1000)/L, wheel verticality α ≤ (0 ~ 2.5/1 000) L. If the deviation exceeds the specified value, the unit area pressure of the wheel tread will result becomes larger, causing uneven wear on the wheel tread and track.
2.2 Reasons for use
1) The RTG yard floor is uneven, the tire pressure of the cart is uneven, or the track of the cart is deformed, which will cause the cart to wander. After a new machine is used for a period of time, the release of stress and accumulated manufacturing errors will also cause the car to deviate. This situation generally rarely occurs again after adjustment.
2) Excessive start or stop operation will cause the wheels to spin and slip, causing the wheels to be out of sync on the tracks on both sides, causing the trolley to deviate.
Based on the above situation, although there are many reasons for the wheel to deviate and chew on the track, manufacturing reasons are one of the main reasons for the trolley to deviate.
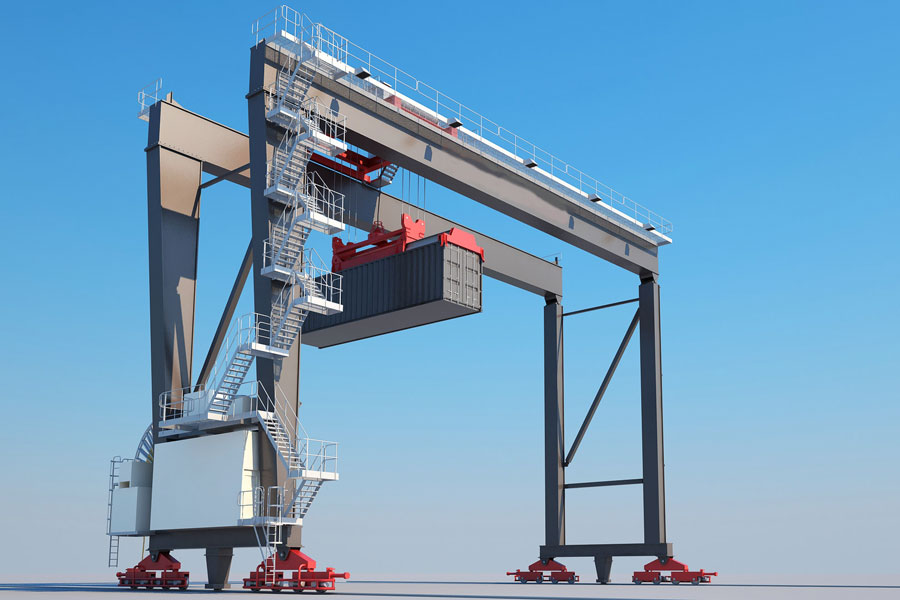
Improve methods
In recent years, with the increasing use of RTG structures for offset rail beam structures (square steel welded rails located inside the box-shaped main beams), the manufacturing requirements have become higher. Let’s take this structure as an example to improve it from the manufacturing aspects such as component manufacturing and processing.
3.1 Process improvement of main beam and track welding
1) Strengthen the feed control straightness of square steel rails (cold drawn processing): up and down, left and right, and 2 directions within a length of 2 m ≤ 1mm. Twist: The twist of any two sections is ≤ 1mm within a length of 1 m, and is not greater than 4 mm within the length of a single track.
2) The track and the main beam panel are welded first to ensure the tight fit between the track and the main beam panel, and then the box structure is formed and manufactured.
3) During the three-sided and four-sided forming processes, the main beam always uses the track surface as the benchmark to control the associated assembly quality. When the final marking is completed, the horizontal level of the upper surface of the track at the zero point is used as the benchmark, that is, Ensure that the reference level of the door frame and the track are consistent when assembling the door frame.
3.2 Pre-bending of main beam
When the trolley load (fixed load + trolley weight + overhead hanger, etc.) is running, the track gauge will become smaller, causing the trolley track to deviate from the center of the trolley wheel, causing deviation. The variation of the trolley at the mid-span and end of the door frame The difference is large. According to calculations and previous manufacturing experience, pre-bending requirements need to be added to the track straightness of the deflection beam.
1) When the structural parts leave the workshop (all accessories have been installed and welded), the side bend of the main beam is controlled at +5 ~ +8 mm (“+” means toward the outside of the door frame), with a smooth transition from the end of the track to the middle of the span, without any Sharp bends exceeding the straightness requirements (±1 mm within 2 m) are allowed.
2) When the main beam and outriggers are assembled on the ground, a tire frame is added to the middle partition of the main beam to eject the upper arch reverse deformation in advance to offset the downward deflection caused by the main beam’s own weight. When welding the joints between the main beam and the outriggers, weld them in a reasonable welding sequence.
3) After the door frame is erected, the trolley track gauge of the door frame is controlled within the following tolerances: ≤ ±3 mm at the inner end: ≤ ±3 mm and in the middle of the span: +4 ~ +12 mm
3.3 Vibration aging treatment of small vehicle frame
Vibration aging treatment technology aims to use professional vibration aging equipment to cause the workpiece to be processed to resonate, and through this resonance method to transfer a certain amount of vibration energy to all parts of the workpiece, causing microscopic plastic deformation inside the workpiece and distortion. The crystal lattice gradually returns to the equilibrium state. It eliminates and homogenizes the residual stress inside the workpiece, ultimately preventing the workpiece from deforming and cracking during processing and use, and ensuring the stability of the dimensional accuracy of the workpiece.
The heavy duty rubber tyre gantry crane trolley frame structure has a large amount of welding, and there is a lot of residual stress in the structure. After the welding is completed, the stress must be eliminated before boring can be performed to prevent coaxiality errors due to welding deformation. Vibration aging treatment of the entire trolley frame can release the residual stress inside the trolley frame components, thereby eliminating or homogenizing the residual stress inside the components to achieve dimensional stability without deformation.
1) According to the characteristics of the RTG trolley frame, when doing vibration treatment, select 4 support points below the main I-beam of the trolley frame, about 1 m from the end, and pad them with cork. The position can be determined according to the specific situation. Adjustment.
2) Clamp the bow clamp of the exciter used for vibration processing on the main I-beam (the specific position can be adjusted according to the actual excitation effect), ensuring that the base of the exciter and the flange plate are tightly fitted, and there should be no iron filings in the middle. If there are any foreign objects, the vibration pickup is sucked tightly on the other side of the small frame.
3) Use cables to connect the vibration exciter, vibration pickup and controller. According to the quality and structural characteristics of the RTG trolley frame, the vibration processing time is selected to be 10 minutes.
4) After the vibration is completed, conduct 100% MT inspection on the main welds (butt welds of the main I-beam and contact welds of the wheel plates). If cracks occur, repair them according to the welding repair process.
3.4 Marking and boring of the axis hole of the small frame
When the trolley frame is under load, the main structure will undergo elastic deformation, causing the wheels to deflect relative to the horizontal plane. For the web-bored trolley bearing structure, when marking the wheel axle hole of the trolley frame, use the method of pressing weight blocks to simulate the load that the trolley frame will bear during actual operation (fixed load + trolley’s own weight + upper frame crane tools, etc.). According to the load distribution of the trolley frame, place the pre-made counterweight blocks in place, put the four corners of the trolley frame in a horizontal state, and then mark and process the shaft holes.
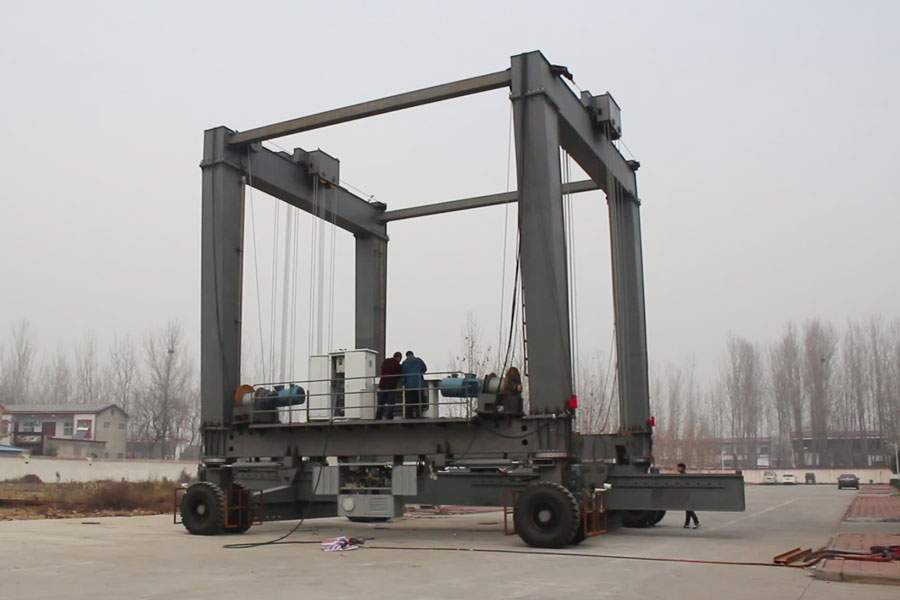
Through the above process measures, the basis for the structural deviation of the trolley track and trolley frame has been improved, creating favorable conditions for wheel assembly and RTG test run, and reducing the difficulty of correcting deviations during the trolley test run.
The wheel deviation of the tire-type gantry crane is a complex problem. There are many influencing factors and ways to improve it. Only in terms of design, manufacturing, installation and maintenance, process control and important indicators should be strengthened in accordance with the requirements of the standards. acceptance. At the same time, manufacturers must add appropriate manufacturing processes and preventive measures based on the structural characteristics of their own RTGs to reduce or avoid the occurrence of rail deviation and ensure the safe operation of rubber tyre gantry cranes for sale.