The trolley operating mechanism of the жоғарғы жұмыс істейтін кран is the transport mechanism of the entire crane, including the motor, controller, coupling, transmission shaft, reducer, angular bearing box and trolley wheels, etc.
The driving method of the trolley operating mechanism
The driving methods of the trolley operating mechanism are divided into two types: centralized driving and separate driving.
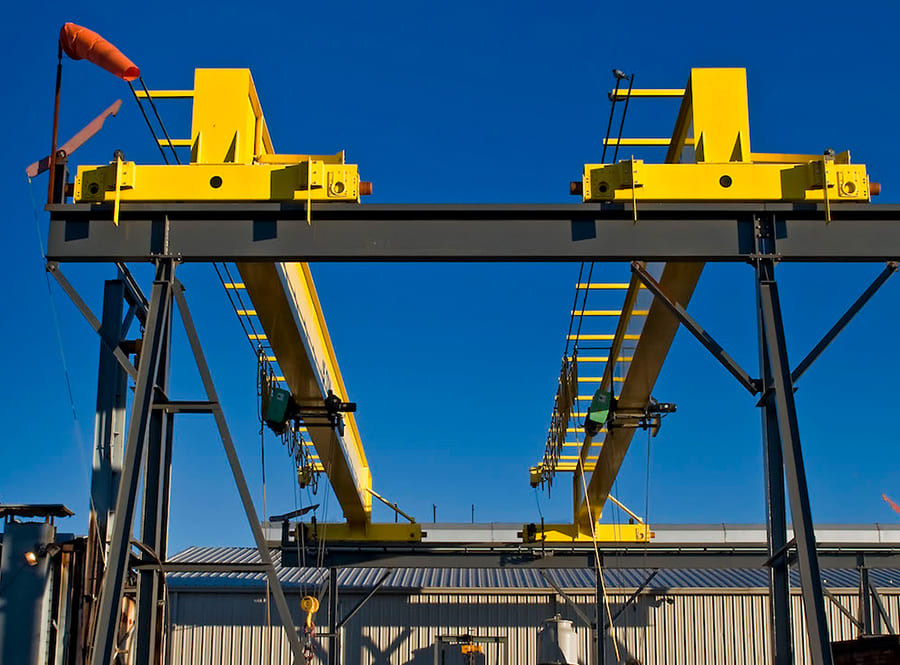
1. Centralized drive
The custom top running crane price driving method in which an electric motor drives the wheels on both sides through a transmission shaft becomes a centralized drive.
Centrally driven drive shafts generally use floating shafts. This is because the floating shaft can compensate manufacturing and installation errors to a certain extent and ensure good transmission performance.
Centralized drive is divided into three types: low-speed shaft drive, high-speed shaft drive and medium-speed shaft drive.
The low-speed shaft driven gear army is installed in the gear box and has good working conditions. However, the low-speed shaft is long and large, and needs to transmit a large torque. Therefore, the dimensions of the shaft, bearings, and couplings need to be enlarged, making the structure bulky. Therefore, it is only suitable for cranes with small lifting capacity and small span.
The advantage of high-speed shaft drive is that the two reducers are close to the end beam, the transmission shaft is in the middle, and the structure is lighter. The disadvantage is that the transmission system requires high processing and installation accuracy, and a protective cover must be installed for safety.
The characteristic of medium-speed shaft drive is that it is driven by an open gear, which has poor working conditions and difficult maintenance, so it is rarely used.
2. Drive separately
The method of driving the cart wheels by two electric motors (with the same specifications) through couplings and reducers is called separate drive. Compared with the centralized drive, the separate drive has the advantages of good grouping, convenient installation and maintenance, large load, even load distribution in the two sets of transmission devices, and small total power required by the motor. Therefore, the separate drive method is currently widely used. However, in use, once there is a problem with the mechanical and electrical devices and they are not repaired in time, it is easy for the two ends to run out of sync.
In the driving mode, there is a high-speed floating shaft between the motor and the reducer. The reduction shaft and the wheels are connected through a coupling. The reducer is close to the end beam, the overall size is small, and the main beam is subject to small torsion. It is currently widely used. form of drive.
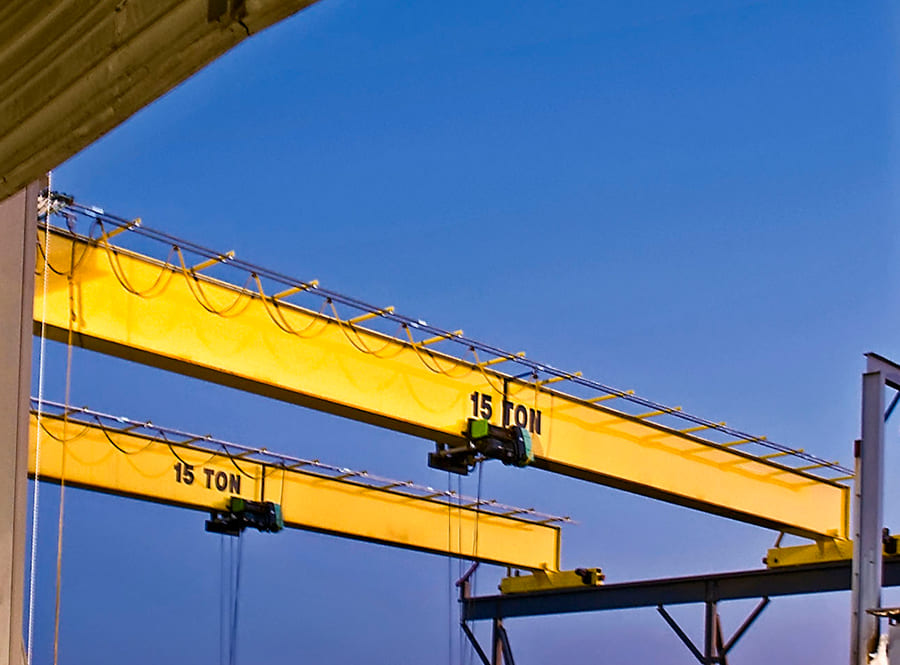
In the driving mode shown, there are floating shafts between the motor and the reducer, and between the reducer and the wheels, that is, the double floating shafts are driven separately. It has better transmission effect and lower requirements for manufacturing and installation accuracy, but increases the structural size.
In recent years, coaxial drive methods have been adopted on bridge cranes, that is, the motor, brake, reducer and wheels are arranged on the same axis.
The sevencrane top running crane for sale coaxial line drive device adopts an electric motor with a brake. The output shaft of the motor is connected to the reducer with splines, and the wheel shaft and the output shaft of the reducer are also splined, eliminating the need for a coupling. This device is small in size, light in weight, and has a small walking platform width. Moreover, industrial top running crane manufacturers is directly connected to the angular bearing box and is out of contact with the walking platform. The bridge is not subject to the torsional load of the cart transmission. Therefore, the coaxial line separate driving method is improved. become more and more widely used.
The reducer in the coaxial drive structure can take the form of two-stage return gear, cycloidal pin wheel and few-tooth planetary gear.