In recent years, with the increasing use of offset rail beam structures (square steel welded rails located inside the box-shaped main beam), the ship building gantry crane have become higher. Let’s take this structure as an example to improve it from the manufacturing aspects such as component manufacturing and processing.
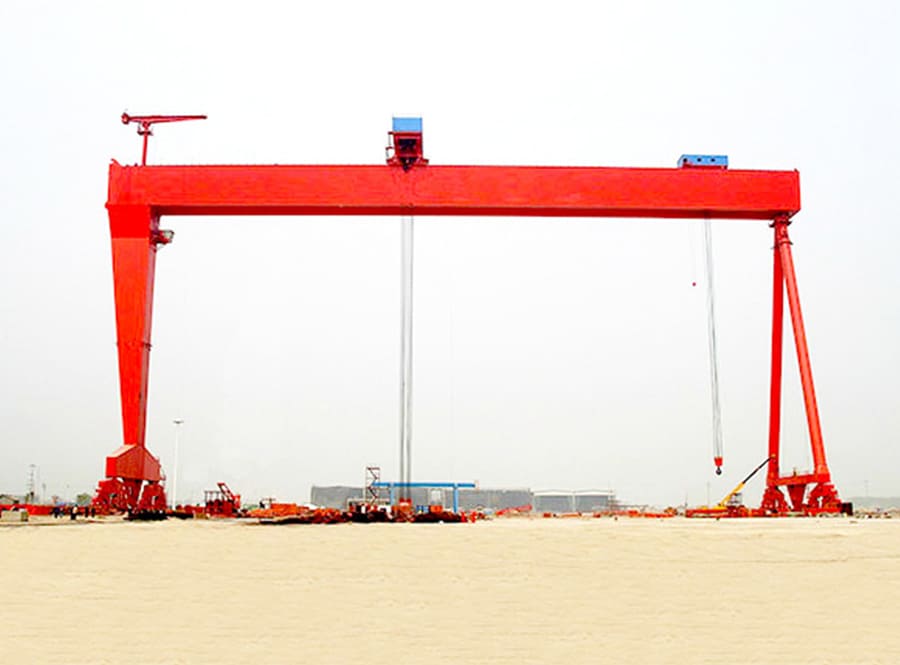
1.1 Process improvement of main beam and track welding
1) Strengthen the feed control straightness of square steel rails (cold drawn processing): up and down, left and right, and 2 directions within a length of 2 m ≤ 1
mm. Twist: The twist of any two sections is ≤ 1mm within a length of 1 m, and is not greater than 4 mm within the length of a single track.
2) The track and the main beam panel of sevencrane ship building gantry crane are welded first to ensure the tight fit between the track and the main beam panel, and then the box structure is formed and manufactured.
3) During the three-sided and four-sided forming processes, the main beam always uses the track surface as the benchmark to control the associated assembly quality. When the final marking is completed, the horizontal level of the upper surface of the track at the zero point is used as the benchmark, that is, Ensure that the reference level of the door frame and the track are consistent when assembling the door frame.
1.2 Pre-bending of main beam
When the trolley load (fixed load + trolley weight + overhead hanger, etc.) is running, the track gauge will become smaller, causing the trolley track to deviate from the center of the trolley wheel, causing deviation. The variation of the trolley at the mid-span and end of the door frame The difference is large. According to calculations and previous manufacturing experience, pre-bending requirements need to be added to the track straightness of the deflection beam.
1) When the structural parts leave the workshop (all accessories have been installed and welded), the side bend of the industrial ship building gantry crane for sale is controlled at +5 ~ +8 mm (“+” means toward the outside of the door frame), with a smooth transition from the end of the track to the middle of the span, without any Sharp bends exceeding the straightness requirements (±1 mm within 2 m) are allowed.
2) When the main beam and outriggers are assembled on the ground, a tire frame is added to the middle partition of the main beam to eject the upper arch reverse deformation in advance to offset the downward deflection caused by the main beam’s own weight. When welding the joints between the main beam and the outriggers, weld them in a reasonable welding sequence.
3) After the door frame is erected, the trolley track gauge of the door frame is controlled within the following tolerance. The end vibration aging treatment technology aims to use professional vibration aging equipment to cause the workpiece to be processed to resonate, and through this resonance method, a certain amount of vibration energy It is transmitted to all parts of the workpiece, causing microscopic plastic deformation inside the workpiece, and the distorted crystal lattice gradually returns to an equilibrium state. It eliminates and homogenizes the residual stress inside the workpiece, ultimately preventing the workpiece from deforming and cracking during processing and use, and ensuring the stability of the dimensional accuracy of the workpiece.
1.3 The small frame structure has a large amount of welding, and there is a lot of residual stress in the structure. After the welding is completed, the stress must be eliminated before boring can be performed to prevent coaxiality errors due to welding deformation. Vibration aging treatment of the entire trolley frame can release the residual stress inside the trolley frame components, thereby eliminating or homogenizing the residual stress inside the components to achieve dimensional stability without deformation.
1) According to the characteristics of the trolley frame, when doing vibration treatment, select 4 support points below the main I-beam of the trolley frame, about 1 m from the end, and pad them with cork. The position can be adjusted according to the specific situation. .
2) Clamp the bow clamp of the exciter used for vibration processing on the main I-beam (the specific position can be adjusted according to the actual excitation effect), ensuring that the base of the exciter and the flange plate are tightly fitted, and there should be no iron filings in the middle. If there are any foreign objects, the vibration pickup is sucked tightly on the other side of the automated ship building gantry crane system.
3) Use cables to connect the exciter, vibration pickup and controller. According to the quality and structural characteristics of the trolley frame, the vibration processing time is selected to be 10 minutes.
4) After the vibration is completed, conduct 100% MT inspection on the main welds (butt welds of the main I-beam and contact welds of the wheel plates). If cracks occur, repair them according to the welding repair process.
1.4 Marking and boring of the axis hole of the small frame
When the trolley frame is under load, the main structure will undergo elastic deformation, causing the wheels to deflect relative to the horizontal plane. For the web-bored trolley bearing structure, when marking the wheel axle hole of the trolley frame, use the method of pressing weight blocks to simulate the load that the trolley frame will bear during actual operation (fixed load + trolley’s own weight + upper frame crane tools, etc.). According to the load distribution of the trolley frame, place the pre-made counterweight blocks in place, put the four corners of the trolley frame in a horizontal state, and then mark and process the shaft holes.
Through the above process measures, the basis for the structural deviation of the trolley track and trolley frame has been improved, creating favorable conditions for wheel assembly and commissioning, and reducing the difficulty of correcting deviations during the trolley trial.
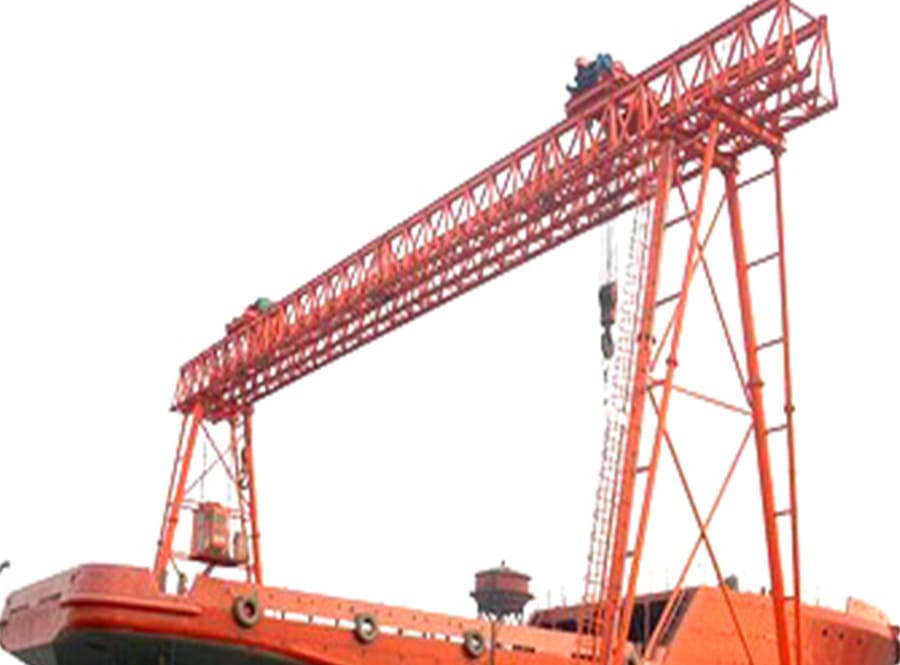
4 Cart correction and adjustment methods
When the car deviates due to factors such as site level, accumulated deviation and stress release, corrective measures need to be taken. The trolley wheel assembly generally adopts the form of adjustable eccentric sleeves to compensate for manufacturing deviations when designing. There are 20 adjustment bolt holes evenly distributed, and each bolt hole can be adjusted by 18°. Through the angle combination of the left and right eccentric sleeves, it can be realized The deflection of the wheels in the horizontal and vertical directions can achieve the purpose of adjusting the deviation of the car.
The way to determine the direction of the car’s deviation is mainly to see whether the horizontal wheel of the car is on the outside or on the inside when it rubs against the track. If it is on the outside when the friction occurs, the car is deflecting inward, and vice versa. After figuring out the direction of the car’s deviation, determine the wheel that needs to be adjusted. Generally, the wheel eccentric bushing on the side with the horizontal wheel is adjusted first.
Before adjusting the wheel eccentric sleeve, you should first use a jack to adjust the trolley until the center line of the wheel is aligned with the center line of the track; then jack up the end beam of the trolley frame so that the wheel is suspended and unloaded; finally, loosen the eccentric sleeve. Tighten the bolts and gradually rotate the eccentric sleeve to adjust. After adjustment, raise the spreader, and then drive the trolley at no-load fast and slow speeds to observe the running status of the trolley. If there is still deviation, you can continue to turn the eccentric sleeve for debugging.
5 Conclusion
As a complex problem, there are many influencing factors and ways to improve the car’s off-track gnawing. Only in terms of design, manufacturing, installation and maintenance, process control and acceptance of important indicators should be strengthened in accordance with the requirements of the standards. At the same time, manufacturers must add appropriate manufacturing processes and preventive measures based on their own structural characteristics to reduce or avoid the occurrence of rail deviation and ensure safe operation.