En comparación con las grúas generales, puentes grúa inteligentes tener inteligencia artificial, que reemplaza o ayuda al trabajo mental humano sobre la base de reemplazar el trabajo físico humano. Integrando sensores con software inteligente de toma de decisiones y grúas se consigue percepción, análisis, razonamiento, toma de decisiones y control.
Función, logrando la interacción e integración entre humanos y objetos, reemplazando la percepción, toma de decisiones y ejecución manual, permitiendo que la grúa se adapte a los cambios en el entorno de trabajo. Su flujo de trabajo es el mismo que el de una grúa general, pero el control inteligente agregado puede reemplazar la visión, el oído y el olfato humanos.
Los órganos sensoriales, como los sentidos y las extremidades, reemplazan el juicio del operador para realizar las acciones correspondientes, completando el reconocimiento, la percepción, la operación y la gestión durante el funcionamiento de la grúa.
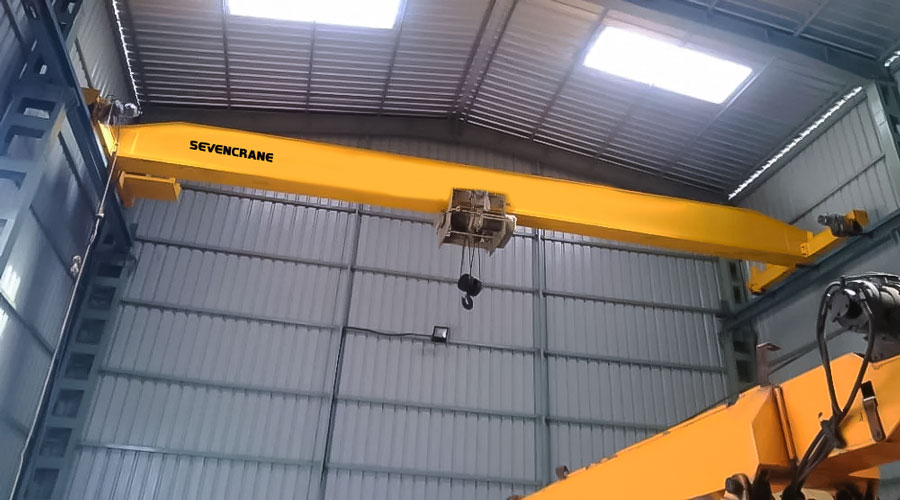
Tecnologías clave de grúas inteligentes
En el proceso de percepción, toma de decisiones y ejecución en nombre del operador, la grúa necesita detectar automáticamente la ubicación de los artículos levantados, identificar y verificar automáticamente los artículos levantados, recoger y colocar automáticamente los artículos levantados, seleccionar automáticamente el ruta de operación, optimiza automáticamente la ruta de operación y supera La oscilación del sistema de elevación flexible puede iniciar y detener con precisión los artículos almacenados en las posiciones correspondientes, y registrar y monitorear el estado de trabajo de su propio equipo durante la operación automática, diagnosticar fallas y alarmas automáticamente . Por lo tanto, la inteligencia artificial de las grúas debe superar varias tecnologías clave.
Tecnología de identificación, verificación, retroalimentación y almacenamiento de información de artículos.
Según la forma, el método de embalaje, el método de almacenamiento y transporte de los artículos que se van a levantar, los artículos comunes que se van a levantar incluyen: rollos (bobinas de acero, rollos de papel, rollos de película, etc.), cajas (contenedores, cajas de material, cajas de transferencia). , etc.), bloques (placas de acero, piezas de acero en bruto, elementos de protección, etc.), haces (tubos de acero, barras de refuerzo, rieles, acero moldeado, etc.), discos (cables, alambrón, etc.), piezas (cubos , bolsas, etc.), raíces (rieles, vigas en I, aceros en forma de H, etc.), etc.).
La identificación, inspección y retroalimentación automática de artículos en varios estados son medios estandarizados de codificación, gestión y transmisión de recopilación e identificación de datos, y son la base para el trabajo inteligente de la grúa. Esta tecnología implica la codificación, recopilación, identificación, gestión y transmisión de datos de información de artículos. Incluyendo reconocimiento de códigos de barras, reconocimiento de radiofrecuencia RFID, reconocimiento de voz, reconocimiento óptico de caracteres, reconocimiento magnético y otras tecnologías de reconocimiento de información de formato específico e imagen, reconocimiento gráfico, reconocimiento biométrico y otras tecnologías de reconocimiento de información de formato gráfico y de imagen. La información del artículo almacenada después de la identificación e inspección debe ser universal, única, estable y no replicable.
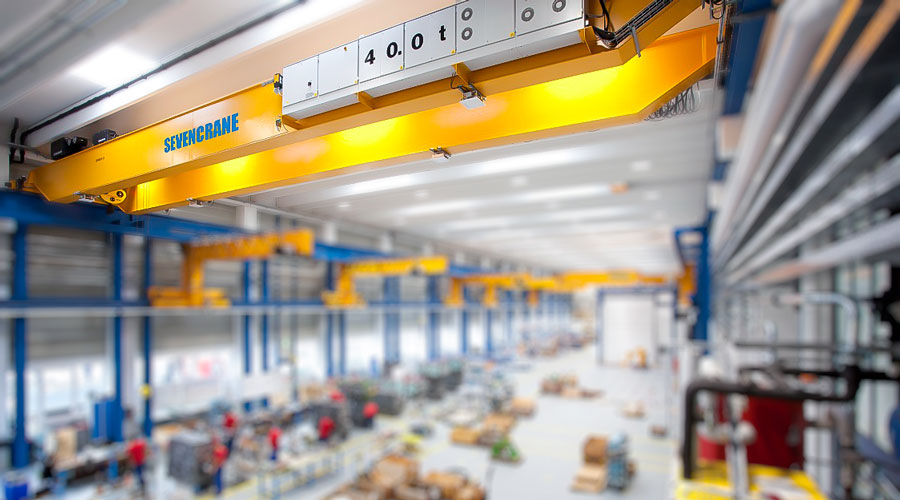
Tecnología de posicionamiento espacial
Aunque algunos productos nacionales de alta gama aplican tecnología de posicionamiento tridimensional, el nivel de posicionamiento está limitado por el error acumulativo de todo el sistema de la máquina y no puede lograr un posicionamiento de alta precisión. En la actualidad, existen dos tipos de métodos de posicionamiento comúnmente utilizados: uno es el direccionamiento relativo, que generalmente se implementa mediante codificadores rotatorios, alcance láser o radar, reconocimiento visual, etc.; el otro es el direccionamiento absoluto, que generalmente se implementa mediante límites de posición. Se implementan interruptores, cables de codificación (bus Gray), codificadores lineales, códigos de barras BPS, cadenas dentadas y direccionamiento absoluto en tiempo real por radio, infrarrojos, radiofrecuencia inalámbrica, GPS, etc. Con el avance de la tecnología de comunicación inalámbrica, la precisión del posicionamiento celular de las redes de comunicación y las tecnologías de posicionamiento inalámbrico en interiores como Wi-Fi, Bluetooth infrarrojo, banda ultra ancha, RFID y ultrasonido se ha vuelto cada vez mayor y se ha promovido y aplicado gradualmente. en el posicionamiento de equipos mecánicos.
La tecnología de posicionamiento de grúas no sólo implica el monitoreo de la apariencia, la detección de espacios libres y métodos de identificación y posicionamiento unidimensionales, bidimensionales y tridimensionales de la ubicación de almacenamiento real de los artículos elevados, sino que también implica grúa aérea dispositivos de recuperación (ganchos, bastidores de carga, ventosas, agarradores, etc.) cubos de agarre, etc.) métodos de posicionamiento y reconocimiento de direcciones unidimensionales, bidimensionales y tridimensionales.
Debido al amplio rango operativo de la grúa, es difícil lograr la precisión de posicionamiento requerida con un único método de posicionamiento. Por lo tanto, la tecnología de posicionamiento integral de "direccionamiento de aproximación relativa + posicionamiento absoluto" se utiliza a menudo para un posicionamiento preciso en áreas grandes y entornos complejos. En comparación con los métodos simples de reconocimiento de dirección absoluta o reconocimiento de dirección relativa y posicionamiento, es más preciso, más estable, más económico, tiene menores requisitos en cuanto a la calidad de los proyectos de ingeniería civil y es más adecuado para entornos hostiles con equipos de elevación.
Dispositivo inteligente de recuperación de objetos
Más de 95% de dispositivos de recuperación de grúas utilizan ganchos, que solo se pueden levantar manualmente para levantar un tipo específico de artículos. La versatilidad es escasa, lo que restringe la mejora de la automatización de los equipos de elevación y manipulación. En el proceso de elevación y transporte de diferentes artículos, como materiales a granel, cajas, paquetes, rollos, etc., las grúas inteligentes deben estar equipadas con dispositivos de recogida automáticos o esparcidores inteligentes, incluidos ganchos de elevación automáticos, ganchos en forma de C y ventosas electromagnéticas. , ventosas de vacío y abrazaderas, vigas colgantes, tanques esparcidores de cajas, cucharas de agarre, agarradores, etc. De acuerdo con el estado de los diversos objetos izados, es necesario desarrollar dispositivos de recuperación automática o esparcidores inteligentes adecuados para aplicaciones de grúa para lograr el acceso automático a la grúa. el eslabón más crítico para que la grúa se vuelva inteligente.
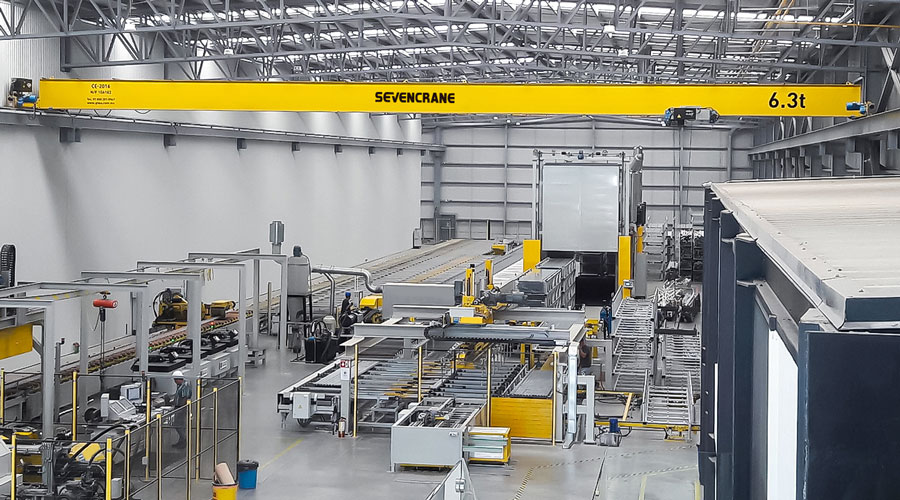
Tecnología electrónica antibalanceo para planificación de trayectorias y sistemas de elevación flexibles
La planificación de la ruta de operación y el control de posicionamiento anti-oscilación del sistema de elevación flexible son condiciones necesarias para la operación de la grúa. Durante la operación de la grúa, la aceleración y desaceleración de camiones grandes y pequeños y el levantamiento de la carga harán que la carga se balancee hacia adelante y hacia atrás, lo que no solo afectará la eficiencia operativa de la grúa, sino que también provocará accidentes. Actualmente, las tecnologías de control de circuito abierto y cerrado se utilizan comúnmente para implementar la planificación del recorrido de la grúa y el control antibalanceo. El método de control de bucle abierto incluye principalmente control anti-oscilación de posicionamiento basado en la configuración de entrada y control anti-oscilación de posicionamiento basado en la planificación de trayectoria. Existen muchos métodos de control de circuito cerrado para lograr la planificación de trayectorias y la estabilización, como la linealización de retroalimentación, el control de programación de ganancias, el control de modo deslizante, el control predictivo, el control difuso, el control de redes neuronales, el control pasivo y otros métodos de control.
Para entornos de elevación y manipulación donde se fijan obstáculos, la planificación de trayectoria estática puede cumplir los requisitos. Sin embargo, cuando los obstáculos en el entorno no se pueden determinar de antemano o cuando varias grúas operan de manera mixta, se debe utilizar un método de planificación de ruta dinámica para obtener una ruta segura en línea en tiempo real. Planificación del camino de elevación. En los últimos años, los académicos han propuesto algunos algoritmos de planificación eficaces para la planificación de la trayectoria de la grúa, como el método de campo de potencial artificial, el algoritmo de punto de referencia probabilístico, el algoritmo de árbol de expansión aleatorio rápido, el algoritmo genético, el algoritmo de colonia de hormigas, etc.
Con el desarrollo de la tecnología de comunicación móvil inalámbrica, se instalan sensores (giroscopios, sensores de aceleración, sensores de orientación, etc.) en polipastos o dispositivos de recuperación para realizar posicionamiento tridimensional, planificación de trayectoria y control anti-oscilación basado en los objetos izados. Ser ampliamente utilizado.
Tecnología de detección de estado y diagnóstico automático de fallas.
El monitoreo de condición se refiere a comprender y dominar el estado operativo del equipo a través de ciertos canales; El diagnóstico de fallas se basa en la información obtenida del monitoreo de condición, combinada con el principio de funcionamiento, características estructurales, parámetros de operación y condiciones históricas del equipo, para analizar posibles fallas. , Pronosticar, analizar y juzgar fallas que han ocurrido o están ocurriendo para determinar la naturaleza, categoría, extensión, ubicación y tendencia de la falla. La importancia del monitoreo de condición y el diagnóstico de fallas es que frena efectivamente las pérdidas por fallas y los costos de mantenimiento del equipo.
Los parámetros de monitoreo comunes que deben monitorearse durante el proceso de monitoreo de la maquinaria de elevación incluyen el peso de elevación, el momento de gravedad: altura de elevación/profundidad de descenso; carrera operativa, amplitud, deflexión operativa del camión; ras; velocidad del viento; Ángulo de rotación; iguales o diferentes 1. Distancia de seguridad del mecanismo de marcha de la vía; verticalidad de los estabilizadores; tiempo de trabajo, tiempo de trabajo acumulado, cada ciclo de trabajo, etc. El estado de monitoreo comúnmente utilizado incluye el estado del motor; estado de los frenos; estado del convertidor de frecuencia; resistencia al viento y estado antideslizante; protección de enclavamiento de límite de puerta y enclavamiento de funcionamiento entre mecanismos; estado de configuración de las condiciones de trabajo; estado del carrete del cable de alimentación; a través del estado del hoyo; Para absorber el sistema de vídeo, la rigidez del puente, la resistencia del sistema de autodetección en tiempo real, etc.
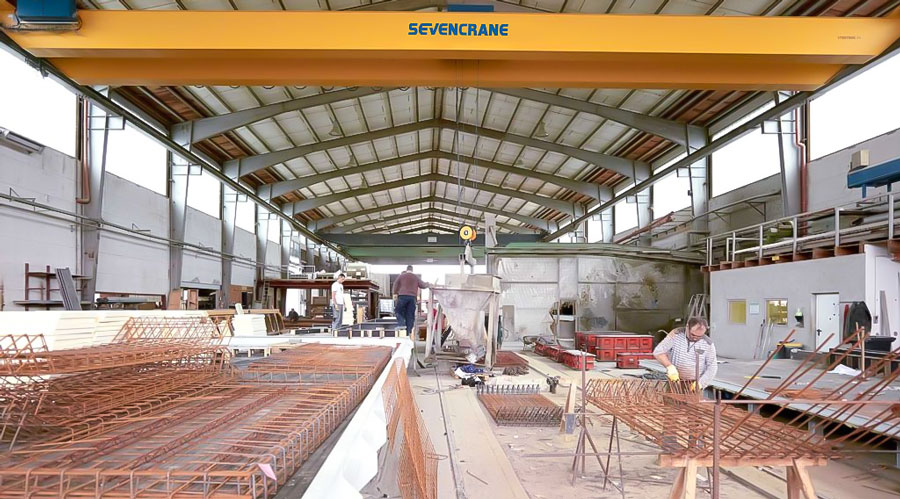
Monitoreo en línea en tiempo real y tecnología de diagnóstico remoto
El sistema incluye monitoreo de sensores, transmisión inalámbrica en tiempo real, gestión de datos, consulta de información, análisis de causa raíz de fallas, análisis de tendencias, diagnóstico experto, predicción y predicción de estado, monitoreo remoto de Internet de las cosas y otras tecnologías. Al instalar puertas de enlace de monitoreo en equipos existentes, los datos se transmiten a través de redes Wi-Fi o 3G para recopilar el estado operativo y las condiciones de falla para lograr monitoreo remoto y gestión visual; integrar el sistema de gestión remota que viene con los nuevos equipos para establecer una plataforma unificada de gestión de equipos; y la integración del sistema de gestión de mantenimiento de activos mejora la eficiencia del mantenimiento y el rendimiento del equipo. Proporcione un mecanismo de cooperación y coordinación de mantenimiento de emergencia en red, obtenga el estado en tiempo real de los equipos a través de la lectura de medidores inalámbricos, genere automáticamente planes de mantenimiento e inspección e implemente gradualmente un mantenimiento predictivo basado en el estado basado en el análisis de datos.
El mantenimiento predictivo realizado a través de una red informática se basa en tecnología de monitoreo de condición y diagnóstico de fallas, basada en el estado real del equipo, y un sistema de mantenimiento que desarrolla planes de mantenimiento predictivo de acuerdo con las necesidades de producción. El objetivo es lograr estacionamiento en tiempo real, reemplazo de piezas correspondientes y mantenimiento de proyectos confirmados. A partir del mantenimiento de fallas actual y el mantenimiento planificado regular, podemos realizar un mantenimiento predictivo futuro, identificar la autenticidad de la falla, determinar el tipo, grado y ubicación específica de la falla y predecir la tendencia de desarrollo de la falla. Detectar señales tempranas de falla de manera oportuna para que se puedan tomar las medidas adecuadas para evitar, frenar y reducir la ocurrencia de accidentes mayores; – Una vez que ocurre una falla, se puede registrar automáticamente información completa sobre el proceso de falla para un análisis posterior de la causa de la falla para evitar que vuelvan a ocurrir incidentes similares. Accidentes; a través del análisis del estado operativo anormal del equipo, revela la causa, el grado, la ubicación y la tendencia de la falla, proporciona una base científica para el acondicionamiento en línea y el mantenimiento de parada del equipo, extiende el ciclo operativo y frena efectivamente las pérdidas por fallas y los costos de mantenimiento del equipo. ; según el estado La información obtenida del monitoreo se combina con el principio de funcionamiento, las características estructurales, los parámetros operativos y las condiciones históricas del equipo para analizar y predecir posibles fallas, lo que puede comprender completamente el rendimiento del equipo y proporcionar evidencia sólida para mejorar el diseño. niveles de fabricación y mantenimiento.
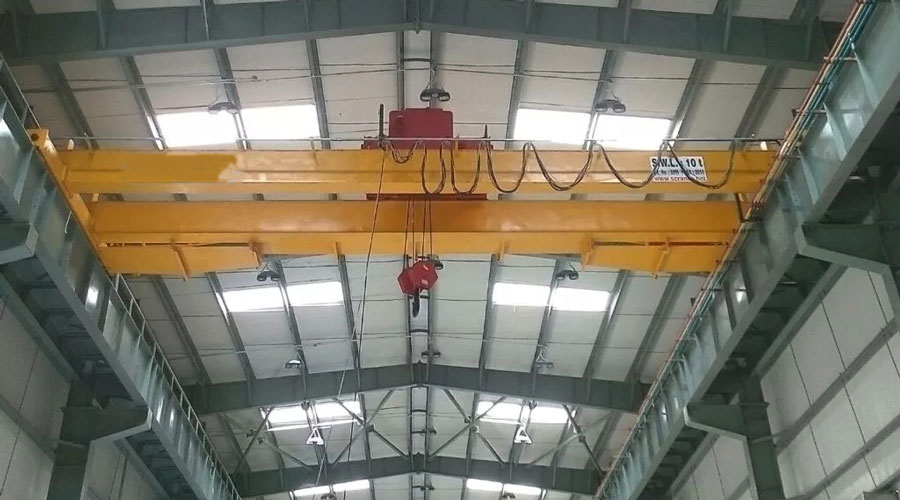
Seguimiento y gestión de juegos completos de grúas puente viajeras
Basado en las formas de apilamiento y requisitos de almacenamiento de diferentes artículos como materiales a granel, cajas, paquetes, rollos, etc., se desarrolla un sistema de monitoreo y gestión MWS para grúas inteligentes basado en las tecnologías clave mencionadas anteriormente, como identificación, posicionamiento, acceso, y seguimiento, incluidos los subsistemas de interfaz y el inventario del espacio de carga. El subsistema de gestión, el subsistema de identificación de artículos, el subsistema de despacho y operación de grúa, el subsistema de posicionamiento espacial, etc., logran el funcionamiento inteligente, eficiente y seguro de la grúa.
En conclusión
La demanda de diversas grúas inteligentes en fabricación inteligente, logística inteligente, mantenimiento inteligente y otros campos aumenta día a día y las perspectivas de aplicación son amplias. Las tecnologías clave anteriores se integrarán en soluciones de aplicaciones de grúas inteligentes en forma de software, nuevos productos, nuevas tecnologías, etc. para formar un conjunto completo de equipos para ingeniería, que se pueden utilizar para transferencia de estaciones en metalurgia, fabricación de papel, automóviles y otros campos de fabricación inteligente y en el campo de la logística. Almacenamiento y mudanza. La grúa inteligente completa automáticamente la operación del flujo del proceso y puede monitorear y registrar el estado operativo de la grúa en tiempo real, proporcionando una mayor eficiencia en el trabajo y menores costos operativos. El sistema inteligente de monitoreo y operación implementa servicios de mantenimiento inteligentes para maquinaria de elevación en servicio, es decir, a través de la detección remota en línea y el análisis estadístico de big data, se logra el mantenimiento predictivo y la evaluación de la vida restante. Los grandes datos acumulados pueden proporcionar una base de datos para el diseño de la grúa, mejorar el nivel general de diseño de la grúa y mejorar de manera efectiva y específica la seguridad y el rendimiento intrínsecos de la grúa.