Dockside gantry crane(commonly known as gantry cranes) are widely used in construction and production, and are mainly used for lifting operations in material yards, steel processing yards, prefabrication yards, and working wellheads in subway station construction. Its flexibility, safety, accuracy, efficiency, durability, and economy are its main outstanding features. However, accidents occur from time to time due to improper management and control in terms of risk identification, equipment control, personnel operation, environmental factors, etc. This article analyzes the current problems and causes of gantry cranes, and through three typical accident cases, proposes safety management countermeasures for sevencrane dockside gantry crane wholesale by “building systems, strengthening standards, and preventing extreme weather” (establishing a sound management system, strengthening on-site standardized management, and preventing extreme weather) .
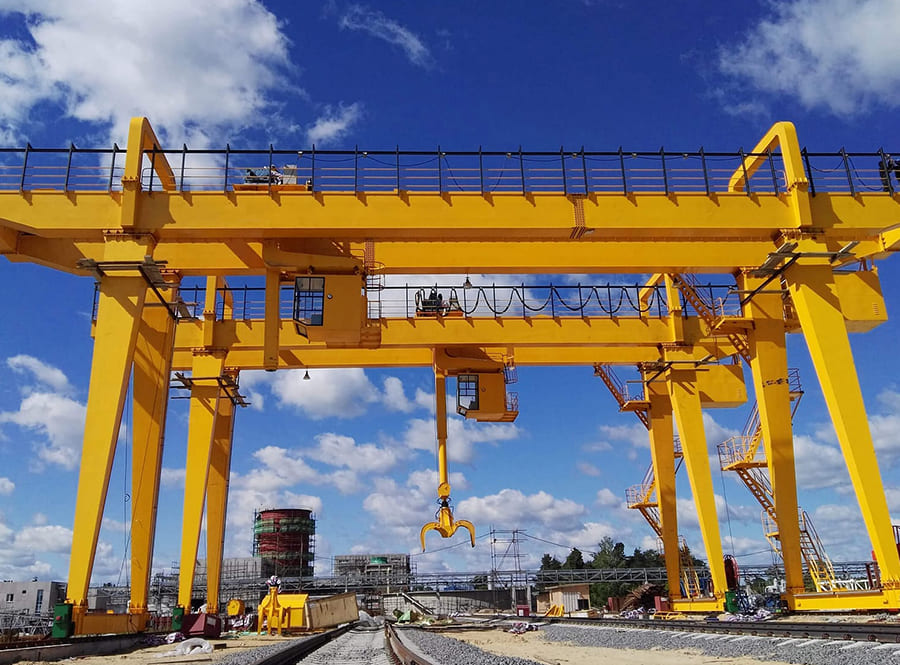
The main safety risks of gantry cranes are concentrated in extreme weather, installation and disassembly, use, maintenance and other process links. In some circumstances, the above risks may coexist and be hidden and sudden.
(1) Insufficient response to natural environmental risks During hoisting operations, construction cannot be performed when lightning, rain, snow, and windy weather are encountered. During lightning, lightning current may hit the top choice for industrial dockside gantry crane causing casualties and damaging equipment. In rainy, snowy and windy weather, the wind will produce strong impact loads on the crane. In severe cases, a major accident may even occur in which the crane is overturned and overturned.
(2) Insufficient identification of risk factors for lifting locks and equipment defects. Suspenders and locks for lifting operations such as slings, wire ropes, shackles, pulleys, etc. are not regularly maintained and inspected in accordance with the requirements of safety technical specifications. There are problems such as serious breakage and cracking. knots etc.
Equipment passages and platform protection are not in place, rails are deformed, safety devices are not installed or damaged, bolt connections are not in place, and there are cracks in major components and other hidden dangers that are not dealt with in place.
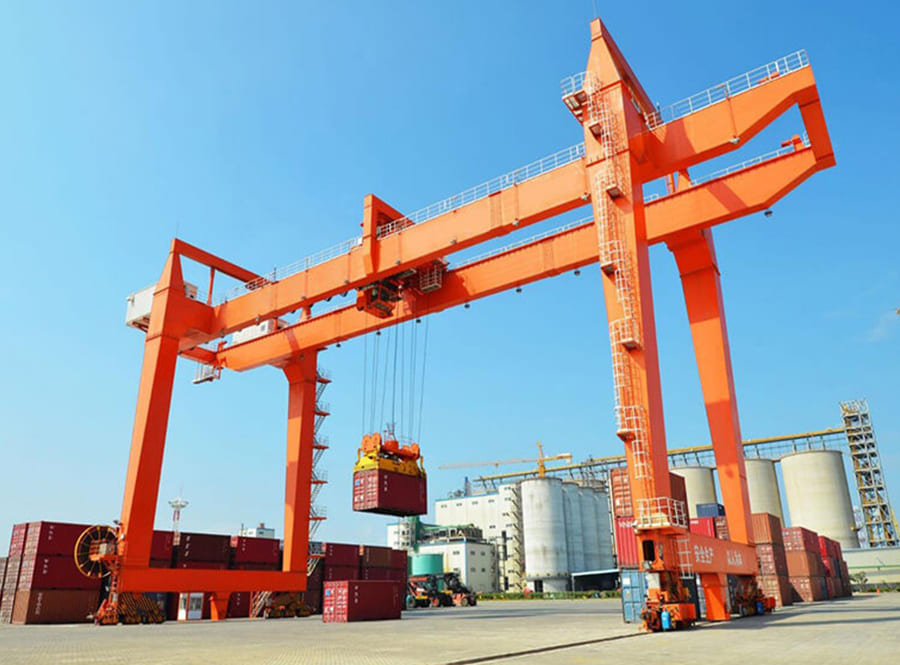
(3) Improper management and operation of operating personnel. Special operating personnel such as lifting machinery drivers, lifting commanders, and rope handlers do not have certificates to work or do not have corresponding skills. The operators failed to conduct pre-operation inspections as required, failed to follow command signals during the operation, failed to make shift handover records after the operation, and failed to take safety measures such as typhoon and wind protection. Routine maintenance was not carried out carefully and hidden dangers were dealt with in a timely manner.