The traditional wire rope flaw detection of port cranes has various disadvantages. The traditional hand-touching and visual inspection of calipers has various disadvantages. At present, weak magnetic wire rope flaw detectors have received more and more attention from customers. There are two types of weak magnetic flaw detection equipment for tire-type shipbuilding gantry crane. , a type of simple portable wire rope flaw detection machine, and another type of online flaw detection equipment for wire ropes fixed on the crane.
The portable wire rope flaw detection ceremony can realize routine testing of the wire rope. The wire rope can be tested at a fixed time when the crane is not operating. The wire rope online monitoring system can monitor the operating status of the wire rope in real time 24 hours a day.
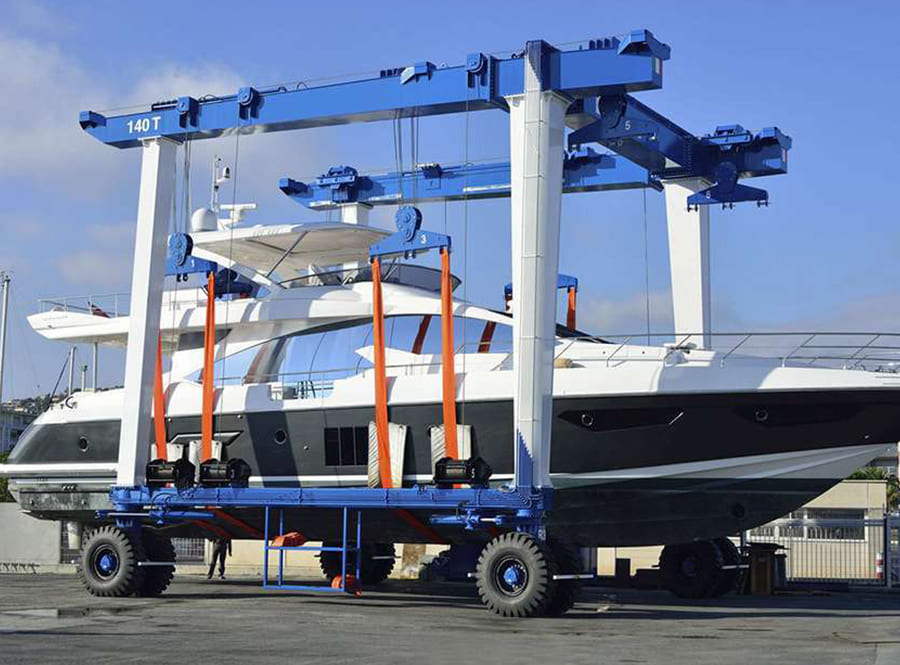
This article mainly describes how to use a weak magnetic memory portable wire rope flaw detector to detect flaws in the wire ropes of tire-type container industrial shipbuilding gantry crane for sale.
Flaw detection position: Generally choose the place on the beam close to the drum
Flaw detection method: asynchronous flaw detection method of magnetizing first and then detecting flaw.
Steps:
1. Raise the wire rope to the upper limit position and install the magnetization meter at the flaw detection position. Then lower the wire rope of automated shipbuilding gantry crane system to the bottom to complete the magnetization work.
2. Instruct the control room to lift about 3 meters to avoid the magnetic pole during calibration.
3. Install the flaw detector for calibration. When calibrating, pay attention to avoid the magnetic poles and the length of the calibration area should not be less than 1 meter. If the consistency of the wire rope is good, then it is easy to select a set of 3 calibration values with a difference of less than 6 during calibration. Just take their average. If the consistency of the steel wire rope is poor and the calibration values are very different, then when selecting the calibration value, you cannot simply find the average value of 3 points. Intensive calibration of the calibration section of the steel wire rope is required. The calibration interval is 5-10cm, the length of the calibration area shall not be less than 1m, record the range of calibration values, and take the average value of the calibration values that appear more frequently as the flaw detection benchmark.
4. After calibration, “special inspection” must be used before flaw detection. During special inspection, there should be no continuous alarm sound with large damage equivalent. The normal situation should be that the instrument has no damage alarm, or there are sporadic and minor damage alarms. If made in china shipbuilding gantry crane equipment is not satisfied, another calibration area must be selected.
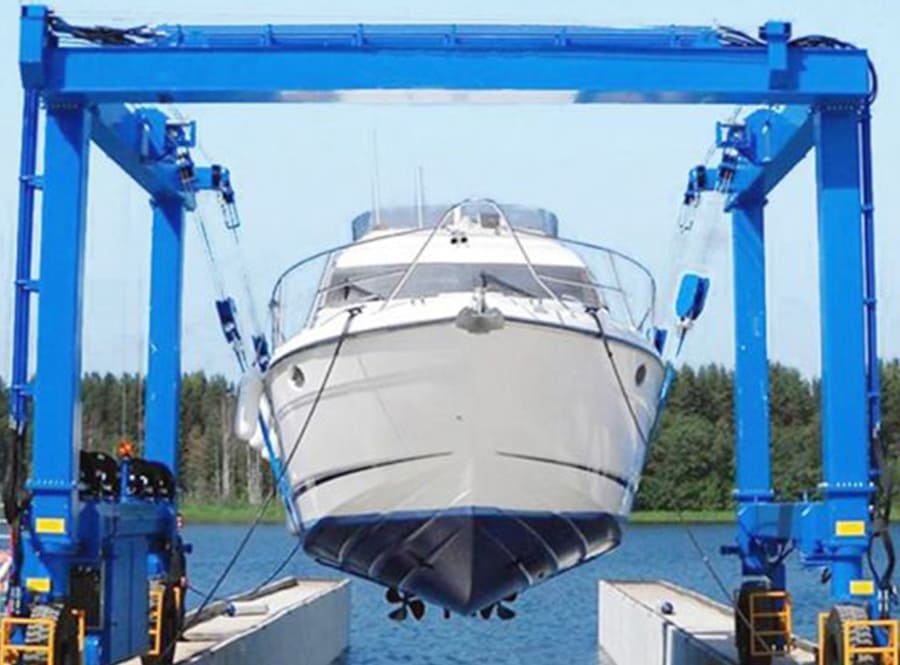
5. Operate the flaw detector to enter the normal flaw detection interface, push the instrument forward slightly to observe whether the recording is normal, and if so, notify the control room to start the vehicle. During the flaw detection process, try to ensure that the flaw detection posture is not changed casually.
Note: Since the port machine has a metal frame, special attention should be paid during magnetization not to let the magnetizer come into contact with ferromagnetic materials near the flaw detection position, so as not to form a source of magnetic pollution and affect normal flaw detection; and avoid contact during the flaw detection process. The magnetic pollution caused by the collision between two adjacent steel wire ropes causes false damage signals in flaw detection.