As an indispensable professional hoisting equipment in industrial production, explosion-proof cranes are mostly used in explosive environments in chemical industry parks. Their safety is closely related to the life safety of enterprises and people. In recent years, with the number of chemical industry parks around the world, An explosion accident occurred, resulting in heavy casualties and huge property losses, which attracted widespread attention from the whole society. Therefore, on the basis of an overview of ex-proof crane, this article briefly discusses the basic explosion-proof principles and explosion-proof technologies of explosion-proof cranes, and then conducts in-depth analysis and research on common problems in supervision inspections and periodic inspections for reference. .
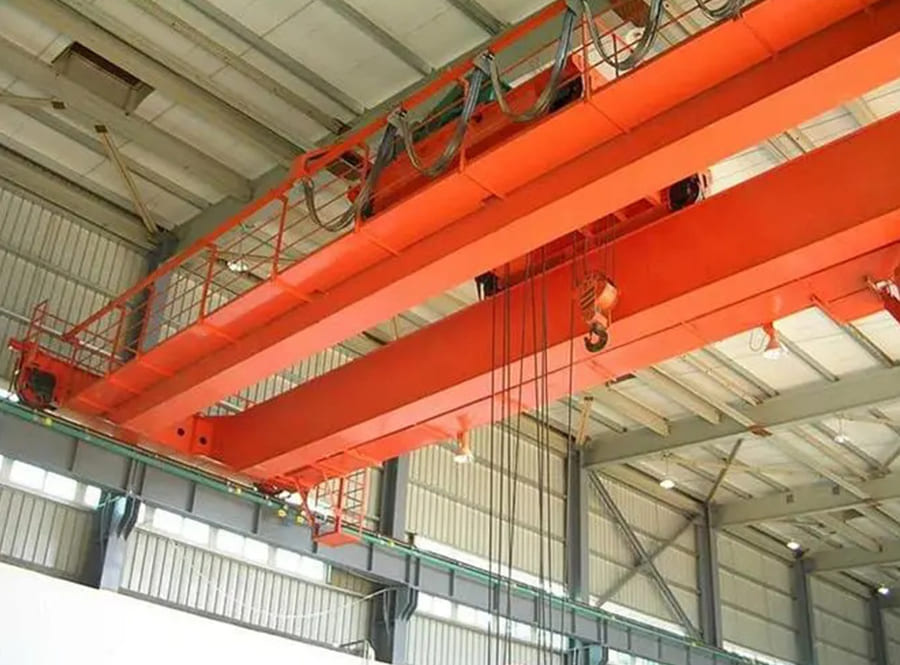
The explosion-proof crane is based on the crane and has the characteristics of reasonable structure, beautiful appearance and strong explosion-proof performance. It is suitable for working in Zone 1 and Zone 2 of explosive gas environment or Zone 21 and Zone 22 of combustible dust environment. It is also suitable for medium , general hoisting operations are carried out in places such as loading, unloading and maintenance of machinery, chemical workshops, warehouses, and stockyards that use flammable and explosive mixtures. Explosion-proof cranes generally work indoors, with a working environment temperature of -20~+40℃ and a working environment air pressure of 0.08~0.11MPa. The categories of explosion-proof cranes are selected according to the classification of hazardous substances, represented by I, IIA, IIB, and IIC (when the IIC environment contains acetylene, special instructions should be noted). The working levels of explosion-proof cranes are A3 to A5.
The sevencrane ex-proof crane wholesale principle of explosion-proof cranes is to use corresponding explosion-proof technology to control or eliminate electrical sparks or mechanical sparks so that they cannot ignite explosive gas mixtures in the environmental area. The core is to prevent the generation of sparks, arcs or overheating. Explosion-proof technology can be summarized into two categories: mechanical explosion-proof technology and electrical explosion-proof technology. At present, most explosion-proof equipment uses PLC top choice for industrial ex-proof crane. This kind of control cabinet has a special shell called an “explosion-proof shell”. This shell can isolate the sparks or arcs generated when the electrical components in the shell are working from the explosive mixture outside the shell. (Detachment), commonly known as explosion-proof function. The shell should also have certain strength requirements (i.e. explosion resistance) to ensure that the explosion pressure generated when the sparks from the electrical equipment in the shell and the arc detonation part enter the explosive mixture inside cannot damage the shell; at the same time, it should also It can prevent the explosion products in the shell from propagating to the explosive mixture outside the shell, and avoid the burning and blasting of the explosive mixture outside the shell. Electrical equipment with flameproof enclosures is collectively called “flameproof electrical equipment”. This type of equipment is widely used in explosive working places such as coal mines because of its outstanding flameproof and CE approved ex-proof crane for sale. PLC explosion-proof control cabinets are generally used in hazardous places such as Zone 1 and Zone 2 or in explosive gas environments of categories IIA, IIB, and IIC with temperature groups T1 to T4. They are also suitable for combustible dust places, etc., and are not sensitive to indoor and outdoor environments. special requirements.
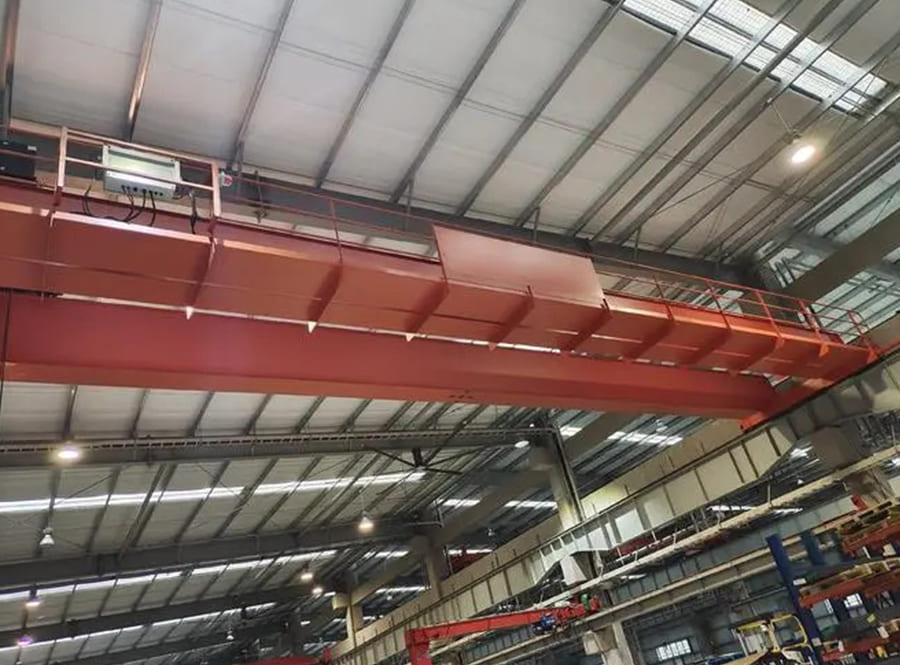
Due to the user’s lack of knowledge about explosion protection and the unclear division of hazardous areas, the selection of explosion-proof cranes is incorrect. For example, if the explosion-proof gas in the on-site environment is hydrogen, an IIB-level explosion-proof crane is selected. Regional division, for example, the dangerous area is Zone 0, but explosion-proof equipment is selected that is only suitable for Zone 1 or Zone 2. When inspecting explosion-proof cranes, the following principles can be followed: the european standard ex-proof crane suppliers type of electrical equipment suitable for zone 0 can be used in zones 1 and 2, and the electrical equipment suitable for zone 1 can be used in zone 2, and vice versa. Can.